After a recent vehicle introduction, discussions about vehicles with 48-volt electrical systems are at an all-time high. Changing standards in vehicles is nothing new. Most cars manufactured before the mid-1950s came with 6-volt batteries. As the need for power and speed from various automobile components has increased, we’re about to witness a change to 48-volt systems. Let’s discuss the implications, benefits and drawbacks of this higher voltage.
Why Did Cars Switch from 6 to 12 Volts?
In 1912, Cadillac installed the first electric starter in its Model 30. Believe it or not, many vehicles before that time were all-electric instead of using internal combustion engines for power. Those vehicles with internal engines had to be cranked by hand. Pushing a button to crank the engine over was convenient and comparatively classy. Six-volt batteries powered these starters.
Fast-forward to the mid-1950s, and the combination of more cylinders with higher compression overtaxed the current delivery capabilities of those 6-volt batteries. To deliver the energy needed to turn the engine over, manufacturers switched to 12-volt systems. Back then, this only affected lighting and maybe an AM radio.
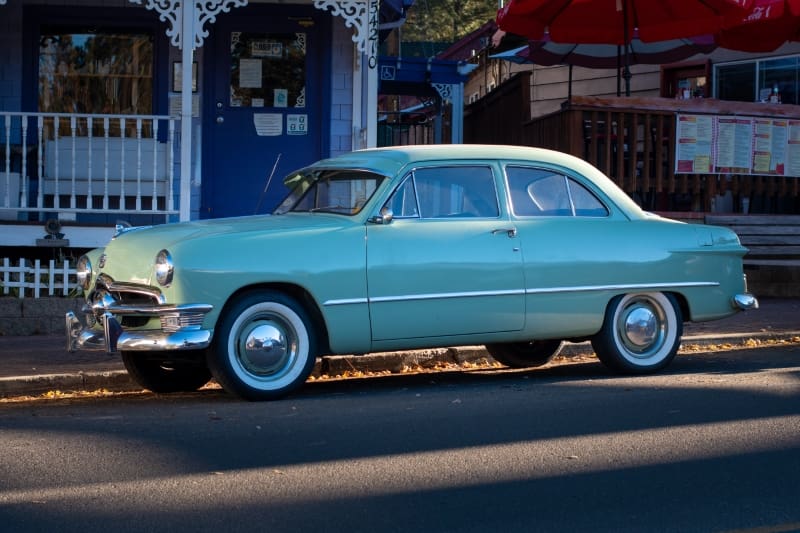
Ohm’s Law and Power Delivery
Let’s talk briefly about Ohm’s law and power delivery in electrical systems. To calculate power in an electrical circuit, we multiply the voltage by the current. If a light draws 1 amp of current at 12 volts, it consumes 1 watt of power. If a starter motor draws 100 amps of current at 12 volts, it consumes 1,200 watts of power. For DC circuits, measuring power draw is very simple.
Let’s look at two hypothetical starter motor examples. Let’s say we need 1,000 watts to crank over an engine. If the vehicle’s electrical system runs on 6 volts, the starter must draw 166.7 amps of current. If our vehicle has a 12-volt battery, we can deliver that 1,000 watts with only 83.3 amps of current.
So why is more current an issue? There are two reasons. First, loads that draw more current require larger conductors regardless of the voltages involved. If we draw 166.7 amps of current through 4 feet of full-size, all-copper 4 AWG cable, we have a voltage drop of 0.179 volt, and 29.82 watts are wasted as heat. If we drop that current draw to 83.3 amps by doubling the supply voltage, the voltage drop decreases to 0.089 volt, and the power wasted is only 7.45 watts. Ideally, we need 2 AWG cable for the 166.7 amp run, which results in a drop of only 0.056 volt and 4.65 watts wasted as heat. For automobile manufacturers, larger conductors mean a significant increase in weight and cost.
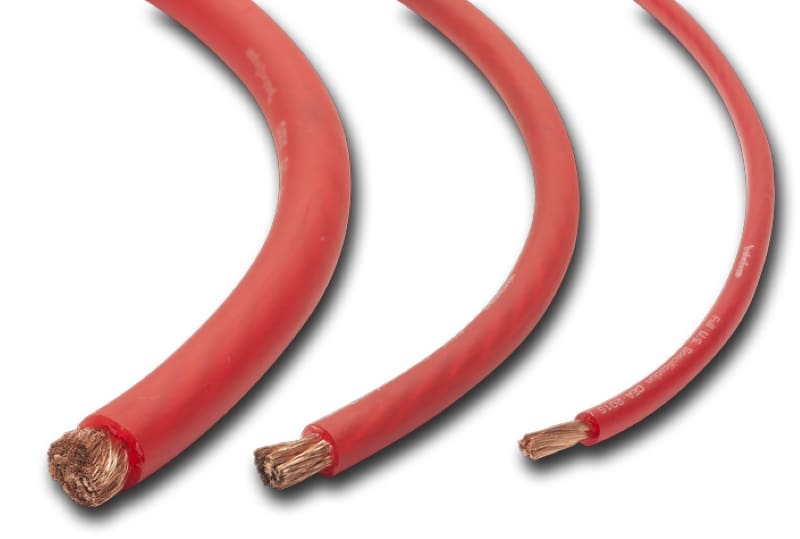
Higher-Voltage Vehicle Electrical Systems Aren’t New
You might not know it, but many airplanes and heavy equipment machinery operate on 24-volt electrical systems. The increased voltage allows for efficient power delivery and reduced wire sizes for airplanes. This reduction in wire size saves weight, which is crucial in airplanes. For heavy equipment, starter motors may need to deliver 9,000 watts of power to crank over a 10.5-liter (638-cubic-inch) six-cylinder diesel engine. Even at 24 volts, that’s 375 amps of current. However, it would be 750 amps at 12 volts. These bulldozers can get away with a single 0 AWG cable with a 24-volt system but would need a 0000 AWG cable of the same length in a 12-volt system to minimize voltage drop.
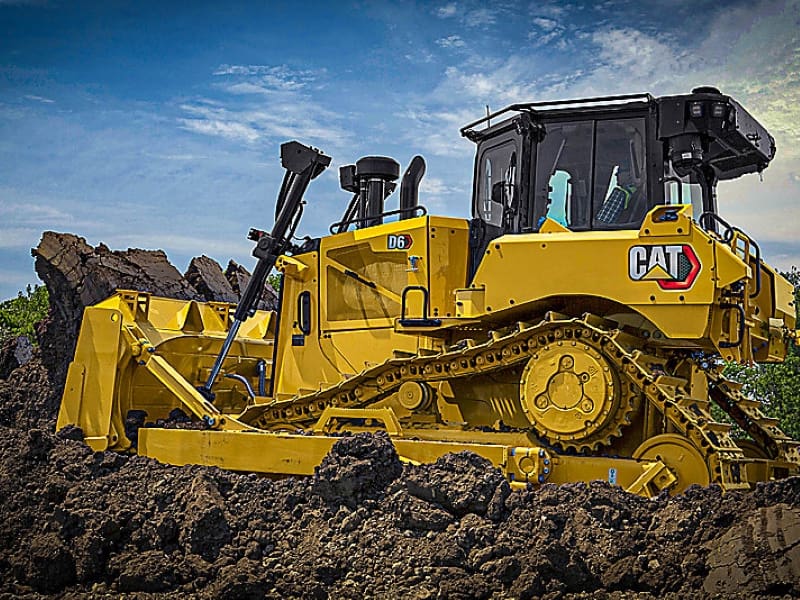
Battery Internal Resistance
Another factor in delivering power from a battery is its internal resistance. Let’s look at a high-quality battery like the Odyssey ODP-AGM96R. This 600 CCA battery has an internal resistance of 2.8 milliohms. That means if a load draws 100 amps of current from the battery, the output voltage will drop by 0.28 volt because of the internal resistance. Let’s put this in the context of a typical vehicle starter motor. Say you have a four-cylinder Honda with a 2.0-liter motor. The starter for that motor is rated for 1,100 watts. That means it draws 92 amps of current after the initial inrush. Our battery voltage would drop by 0.257 volt from the battery’s internal resistance.
What if the same starter could run on two 12-volt batteries wired in series? We still need 1,100 watts of power, but we have 24 volts of potential. The internal resistance of the batteries is the same, but the current draw is now 45.8 amps. We only drop 0.128 volt from internal resistance. The batteries don’t have to work as hard and won’t get as hot to do the same work. Plus, we can now wire the starter with 6 AWG wire, have less voltage and power loss in the conductors, with a wire that’s 37% lighter.
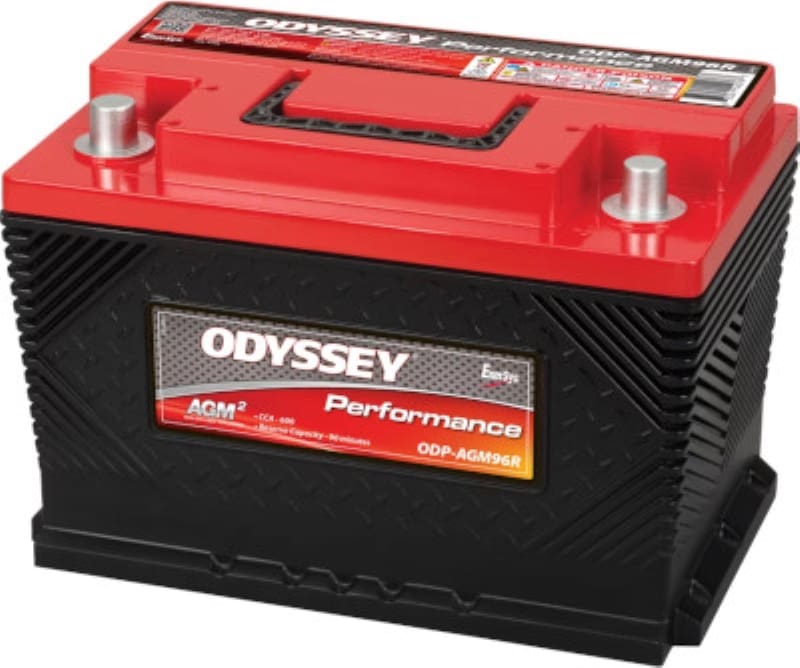
Why Do Vehicles Need 48-Volt Electrical Systems?
We’ve shown that conductor size and weight reduction are significant benefits of higher-voltage electrical systems. But why do we need all this power? The outrageous Hummer EV uses an electric motor to actuate the rear wheel steering. That motor needs to turn quickly to respond to input from the steering wheel. The original heater in the 2019 Tesla Model 3 drew 2,170 watts of power. The heat pump in the 2021 Model 3 draws only 735 watts. However, both are significant loads.
Here’s an excellent example of why new vehicles may require higher-voltage electrical systems. In the case of cars and trucks that use brake-by-wire systems, the issue is often speed rather than outright power. An actuator running on 48 volts can respond faster than one on 12 volts. The Tesla Cybertruck uses electric actuators for the front steering. They must keep up with input from the steering wheel, which is paramount to driving the vehicle safely. Delivering the required response speeds reliably can only happen with higher-voltage electrical systems.
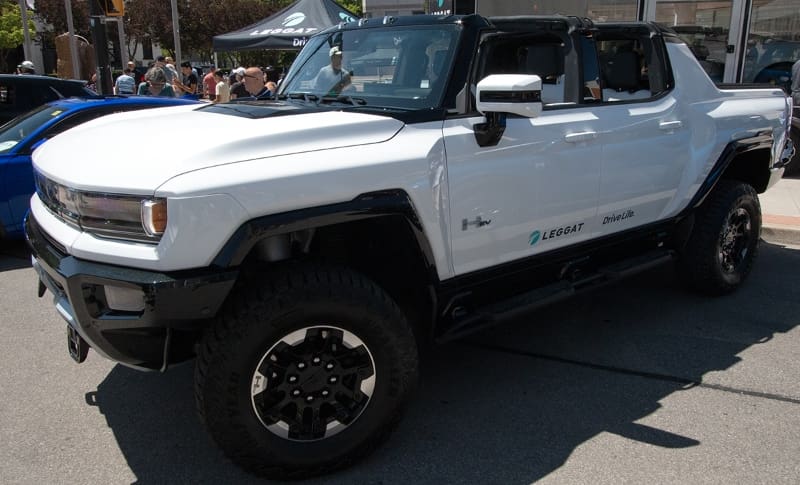
Enthusiasts of radio-controlled planes and cars use high-voltage servos to improve the response time of flight or steering inputs. Here’s an example of two similarly powerful servos: The red MKS DS9910 servo below can provide 361.1 ounce-inches of torque and swing through 60 degrees in 0.159 second when powered with 6.0 volts. The black HBL575 servo can accept up to 8.4 volts, provide a similar 333.3 ounce-inches of torque, and rotate through 60 degrees in 0.06 second. That’s 2.65 times faster while offering very similar stall torque.
48-Volt Electrical Systems and Audio Upgrades
Higher electrical system voltage can only be a benefit to audio systems. As it stands, a lot of audio system design choices at the OEM level consider the limited voltage available to power the amplifier. For example, you often see factory-installed subwoofers with two 2-ohm voice coils, each wired to a separate amplifier. This twin-amp configuration is an easy way to deliver a specific amount of power without creating a complex and expensive amp with a large step-up power supply. Several aftermarket subwoofers like the Rockford Fosgate P500-12P and Audison APBX 8 AS2 use a low-impedance subwoofer and an amplifier without a step-up power supply to decrease complexity.
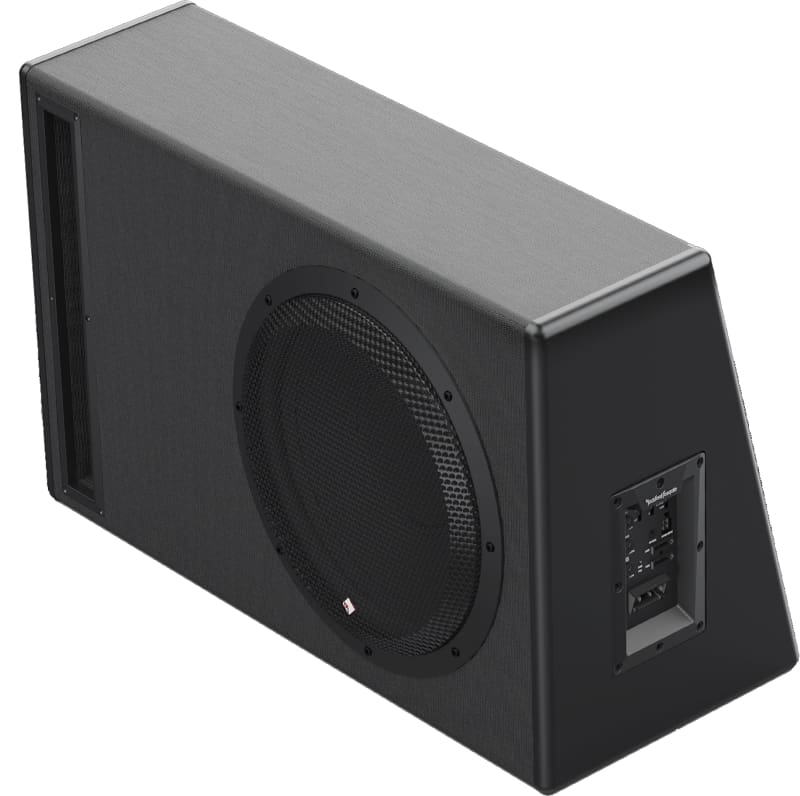
High-voltage amplifiers are nothing new. Many brands offer 24-volt amplifiers for marine applications. Some Brazilian SPL amplifiers forego the power supply stage in their amplifiers in lieu of having the installer wire batteries in series to feed the amp. Some amplifiers can accept as much as 300 volts DC and produce a brain-bending 40,000 watts of power. That would be 24 batteries wired in series. Aside from not needing all the power supply components, the amp can make that power with a 130 Amp fuse. Remember, more voltage means less current. Crazy!
Returning to the real world, let’s say we want to add a 1,000-watt amp to a vehicle with a 12-volt electrical system. If it’s a high-quality amp with an efficiency above 90%, it will draw about 93 amps of current. If you choose a poorly designed amplifier, the efficiency might be down around 65%. As such, that amp would make the same power but would need 128 amps of current from the electrical system. The efficient amp would work with a 16-foot run of 4 AWG wire, and only 0.1 volt is wasted across the wire. The less efficient amp needs a 2 AWG wire to keep the losses to about the same level.
What if we bump the electrical system to 48 volts? The good amp will draw 23 amps of current at full power and can use a 10 AWG wire. The poorly designed amp will draw 32 amps of current and needs 8 AWG power. These are significant reductions in current draw and cable size.
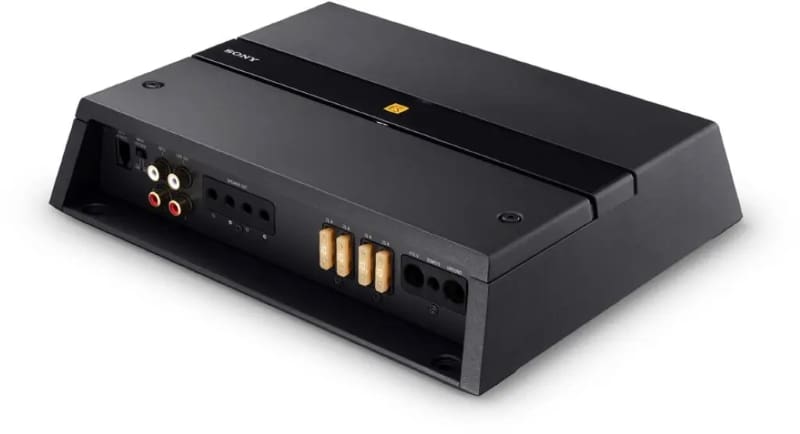
Amplifiers With No Power Supply
If our vehicles had a 48-volt electrical system, how much power could an amplifier produce without a step-up power supply? Let’s assume we swing the voltage through 46 volts to account for some losses attributable to component biasing and such in the amplifier. We’d have an RMS voltage of 16.26 volts, producing 66.1 watts to a 4-ohm load, 132 watts to a 2-ohm load and 264 watts into a 1-ohm load. It would be easy to have a multichannel DSP amp with six or eight channels that produce 66 watts of power, and it wouldn’t need the components required for the power supply. A matching subwoofer amp with channels designed to deliver 260 watts each would likely fit in the same size chassis. Keep in mind, the limiting factor in power production is keeping the amp running reliably, so the chassis needs to dissipate any heat generated in the output circuitry.
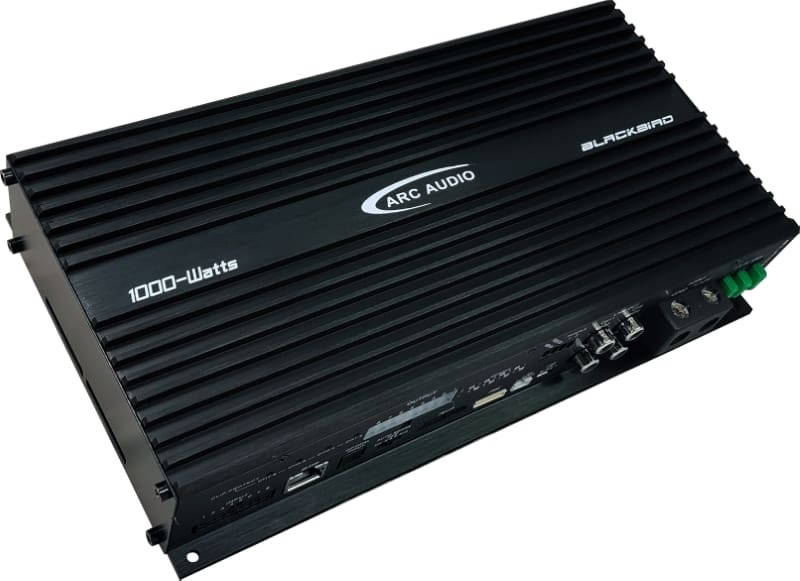
Is a 48-Volt Electrical System Safe?
I chatted with a few industry friends about the evolution of vehicles to 48-volt electrical systems. More than once, the topic of safety came up. After some research, 48 volts is right on the border of what’s considered safe. The term “high voltage” applies to DC voltages above 60 volts in the automotive industry. Vehicle manufacturers deliberately chose 48 volts to avoid high-voltage systems’ safety and handling requirements.
Will you get a shock if you touch 48 volts? The consensus is that there are a lot of variables. You are likely safe if your hands are dry, but you will feel it. If your hands are sweaty, it could be dangerous.
Another problem with DC voltages versus the AC we have in our homes is that a shock from DC causes you to grab onto the source tighter. On the other hand, shocks from AC can be more harmful to your heart. Avoiding all risks is the best approach.
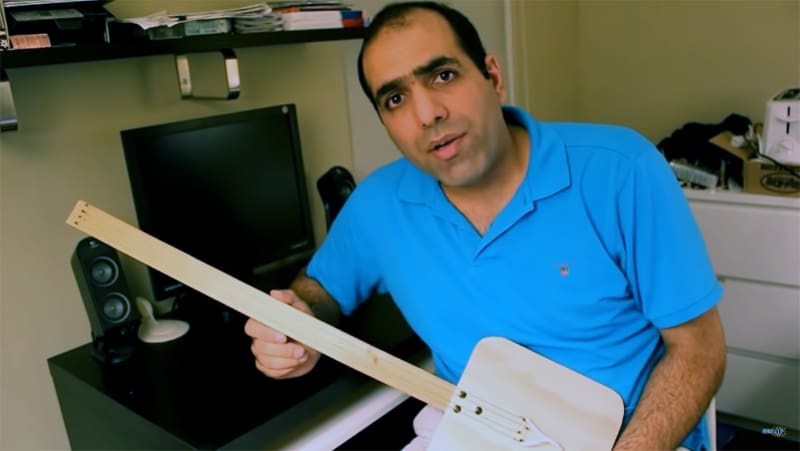
48-Volt Electrical Systems are Coming
It’s not unreasonable to predict that the next generation of each new vehicle will include 48-volt electrical components, at least on some systems. Will the trailer lighting connector and cigarette lighter adapter be 48 volts? Probably not for a long time. However, starter motors, actuators, blower motors and audio system amplifiers will likely use this higher potential to reduce their current draw and wiring requirements. It will be interesting to see how the automotive industry evolves.