Many years ago, I read an article that said the difference between a tube amp and a solid-state one was primarily in their distortion characteristics. Even though I thought about the statement repeatedly, I was mistakenly correlating the presence of distortion with what happens when we try to over-drive the output of a source unit or amplifier. As with any complex topic, it took some additional education and research before it became clear to me what the author was talking about. Now it’s time to share that information with our valued readers and car audio enthusiasts. Let’s talk about audio component distortion and how it changes the sound of what we hear.
What Is Distortion?
Any time the output of a device doesn’t 100% match the input, we consider that device to have added some distortion. For a high-end amplifier, the difference might be small amounts of noise, some harmonic distortion and some intermodulation distortion. We’ve talked about all these concepts at length in many articles.
What wasn’t clear to me when I first read the statement about the difference between tube and solid-state amplifiers was that distortion happens all the time – not just when the amplifier is overdriven to the point of clipping. If you read any of the Test Drive Reviews we publish here at BestCarAudio.com, you’ll see I include distortion characteristic graphs with all amplifier tests. These graphs show the amount of harmonic distortion added to the audio signal at different levels or at a level where the amplifier operates most frequently.
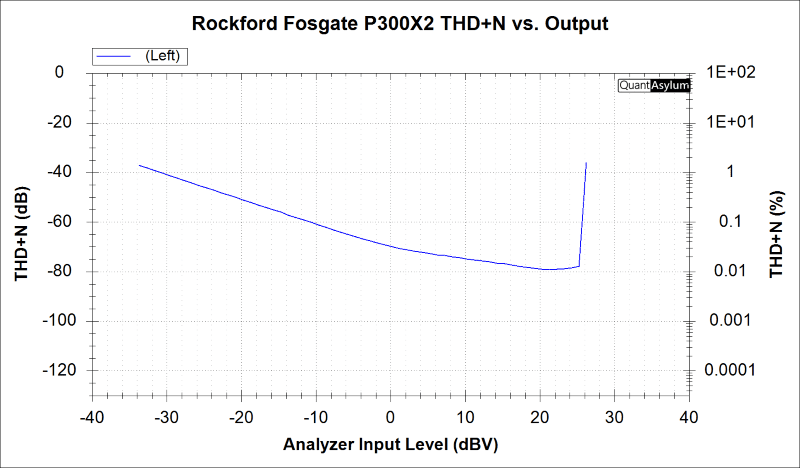
The graph above shows the typical harmonic distortion and noise curve for a Class A/B amplifier. As the output signal amplitude increases, the noise and harmonics’ effect on what we hear decreases. Look at the 0 dBV level – the distortion is at -70 dB. This measurement means there is harmonic content at 2000, 3000, 4000, 5000 hertz and higher that add up to being 70 dB quieter than the audio test signal at 1000 Hz. This amplifier has a very flat distortion versus frequency curve, so if I test it at 100 Hz, the harmonics at 200, 300, 400, 500 and so on would also add to be about 70 dB quieter than the main signal. It’s worth noting that the 0 dBV level equates to an output of 1 volt, which is 0.25 watt into a 4-ohm load. If you’re listening to your sound system at moderate levels, this is likely around the power the amp is producing.
Suppose I increase the input signal such that the amp is producing 25 dBV (which is just a hair under 80 watts). In that case, the combined measurement of distortion harmonics and noise amplitude drops to about 78 dB below the test signal. In most amplifiers, noise is typically fixed around a certain amplitude. Increasing the audio signal’s amplitude helps drown out that noise, leaving us with harmonic distortion as our primary concern.
Source units and signal processors have the same types of characteristics as amplifiers. They all add some amount of noise and harmonic distortion to the audio signal they reproduce. The amount of distortion will likely vary depending on the signal’s amplitude. A graph showing the behavior of different frequencies and amplitudes provides a significantly clearer image than attempting to quantify the product’s quality with a single number.
To summarize, all audio components, from tiny $5 Bluetooth speakers to amplifiers and source units costing thousands of dollars, all add distortion all the time. What separates one from another is how much noise and distortion they add.
Speakers Add More Distortion Than Electronics
If you’ve paid attention to the dozens of articles we’ve published that talk about audio system upgrades, you’ll recall that I put a significant emphasis on choosing high-quality speakers for any audio system. Unfortunately, many people in all aspects of the audio industry can’t grasp that speakers are typically the leading contributor of distortion to what we hear. On top of that, the louder we play our music, the worse it typically sounds.
Why? All speakers, from every manufacturer and in every size, become increasingly non-linear at higher output levels. If you listen to music at 60 or 70 dB, then the speakers’ cones are barely moving and everything usually sounds fine. Subwoofers, woofers and even midrange speakers start working hard once you start to turn up the volume. Variances in magnetic field strength and suspension compliance at different cone positions mean sound that’s reproduced doesn’t track the original audio signal.
You know when those guys with two dozen PA speakers in their doors drive by, and the music sounds really harsh? That’s NOT the sound of loud; that’s the sound of distortion. If they’d chosen high-quality speakers with good power handling and excursion characteristics, flat frequency response and distortion-reducing technologies like shorting rings and copper T-yoke caps, their systems would play just as loudly but sound great.
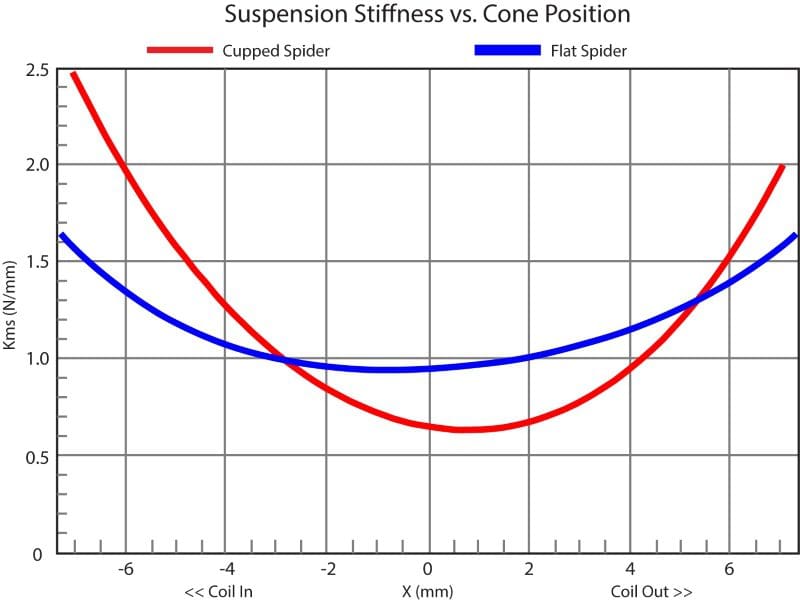
Engineering test systems like those from Klippel GmbH can, when used properly, tell an engineer a great deal about the design of a speaker. For example, look at the graph above. The blue curve shows a much more linear compliance curve than the red. The blue curve is also more symmetrical than the red with respect to forward and rearward cone excursion. In both cases, the minimum compliance isn’t centered. The minimum on the blue curve is at 0.9 mm inwards, and the minimum of the red curve is at 0.75 mm of the coil out. All of these changes in compliance result in the speaker not responding to the input signal linearly. As a result, harmonics are added to the output.
The same issue happens with voice coil inductance. As the coil moves deeper into the speaker, more metal (the T-yoke) is inside it, so the inductance increases. When the cone moves outward, the inductance decreases. The result is a change in the speakers’ frequency response, depending on how loudly it’s played. Can you fathom someone trying to calibrate the response of that system with a DSP?
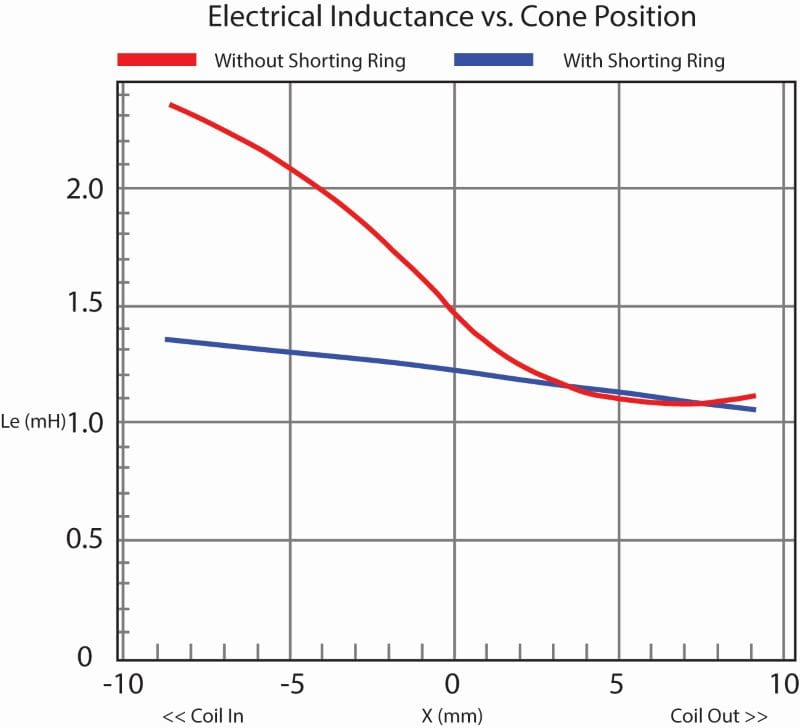
Many companies don’t fully understand how speakers work and choose to ramble on about supposedly exotic cone materials. The fact that they emphasize these technologies in subwoofers is even more comical. Genuine high-fidelity speaker performance starts with a high-quality motor design. Can you imagine if Ferrari, Bugatti, Koenigsegg, Lamborghini or Rimac talked about the colors of their cars but ignored the drivetrain and suspension design? Suddenly I’m having flashbacks to Pontiac Fiero’s with Ferrari-esque body kits from the late ’90s. Speaker cones should be adequately rigid, properly damped and of a specific mass to function correctly. The true sound quality comes from suspension component selection and linearity-improving, distortion-reducing technologies like flat linear spiders, shorting rings and copper T-yoke caps.
Choose Your Car Audio Upgrades Wisely for the Best Sound
Every audio component from every company and at every price point adds some distortion to the audio signal. If your goal is to create a truly high-end audio system, the priority should be to select components that offer low-distortion designs. This isn’t an easy task as most companies don’t fully understand the related concepts, so they can’t implement them or explain how they work.
So, how do you get the very best? You choose with your ears. Learn how to audition audio components. You’ll need to listen to dozens if not hundreds of systems under very controlled conditions to learn what’s right and what’s unfavorable. Start your search at your local specialty mobile enhancement retailer.